Bore inside diameter must correspond to H8 tolerance group conditions specified in ISO 286-2.
Bore-seal tightness
The outer diameter of the seal must be larger than the inner diameter of the bore in which it is mounted in order to provide expecting static sealing, and this difference called as ‘interference’ or ‘tightness’ should provide reasonable stability, and also enables a feasible installation.
Depending on whether the outer diameter is flat rubber, recessed form (knurled) rubber and metal, determined tightness and the circularity/ovality values of the outer diameter of the seal are shown in the table.
(1)Roundness is calculated according to the result of O.D.maks - O.D.min obtained from measurements made at equal intervals of three or more numbers.
Bore material
Usually, steel or cast iron is used as bore material. In some particular applications, aluminum or plastic derivatives may also be preferred. Attention should be paid to a possible reduction in tightness due to the different thermal expansion coefficients, especially at high temperature changes between bores, which are processed from materials other than general steel materials, and seal. Such thermal expansion differences are high, rubber covered seals should be preferred.
Surface quality
For the surface quality of the housing bore, the recommended roughness values according to the outer diameter material of the seal are shown in the table. Especially when metal-cased seals are used, it is even more important that the inner surface of the housing bore should be free free from inconvenience such as scratch, burr, dirt and so on.
|
O.D. rubber (um) |
O.D. metal (um) |
Rz |
10 – 25 |
6,3 -16 |
Ra |
1,6 – 6,3 |
0,8 - 3,2 |
Rmax |
≤ 25 |
≤ 16 |
Housing Bore chamfer/radius
To prevent damage to the rotating shaft seal during installation, entry parts of the housing bore should be chamfered. No sharp surface should be left on the corners where it is chamfered, and should be free from burrs and rounded.
At the joining edges, where the seal is seated in the bore at the end of the installation, corners with the low radius as possible are desired. The different chamfer and radius values suggested by the seal height can be seen in the table.
b
(mm) |
t1 min.
(mm) |
t2 min.
(mm) |
r2 max.
(mm) |
7 |
5,95 |
7,30 |
0,50 |
8 |
6,80 |
8,30 |
0,50 |
10 |
8,50 |
10,30 |
0,50 |
12 |
10,20 |
12,30 |
0,70 |
15 |
12,75 |
15,30 |
0,70 |
20 |
17,00 |
20,30 |
0,70 |
Static shaft misalignment
The difference (offset) between the shaft and bore axis that does not fully overlap is known as static shaft misalignment various machining and assembly errors cause this. Ideally, the axes of the shaft, bore and rotary shaft seal are expected to coincide.
The static misalignment causes one side of the sealing element to contact the shaft surface more than it should, and one side less than it should. Abrasion characteristics change depending on this. Part of the seal lip is abraded faster, total seal life is consumed faster than expected.
The maximum permissible misalignment values depending on the shaft diameter can be seen in the related graph.
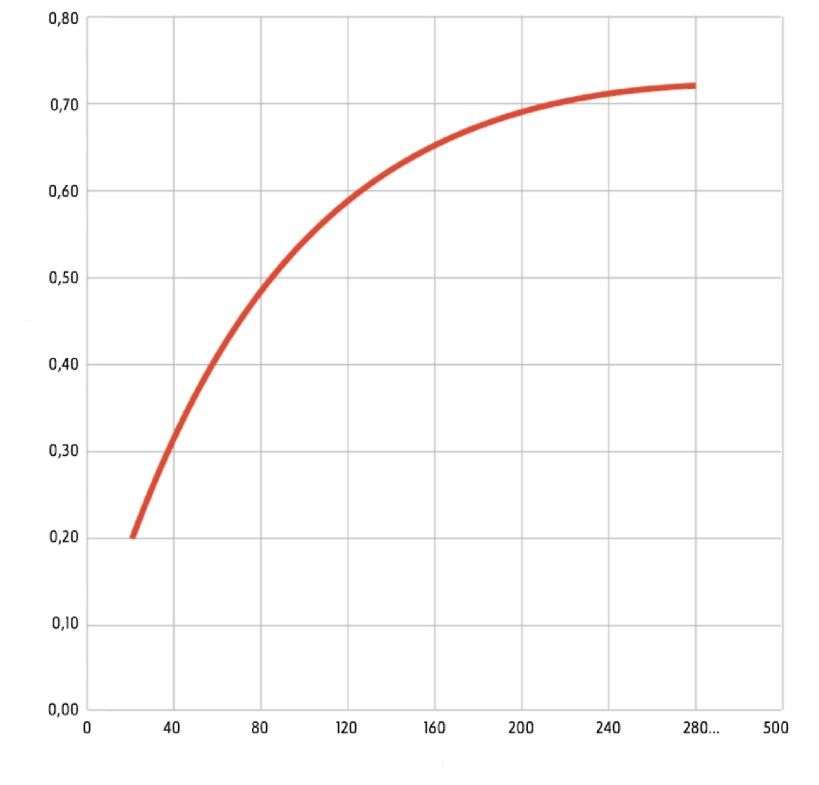